Bi-metal Sliding Bearing Bushing Dimensional Inspection
It is not possible to accurately measure the external and internal diameters of a wrapped bush in its free condition. At the free state, a wrapped bushing will not be perfectly cylindrical. The bush will conform to the housing when the butt joint is tightly closed. For this reason the OD & ID of a wrapped bush can only be checked with special gauges and test equipment. The checking methods are defined in IS03547 Part 1 and 2 and ISO 12306 respectively.
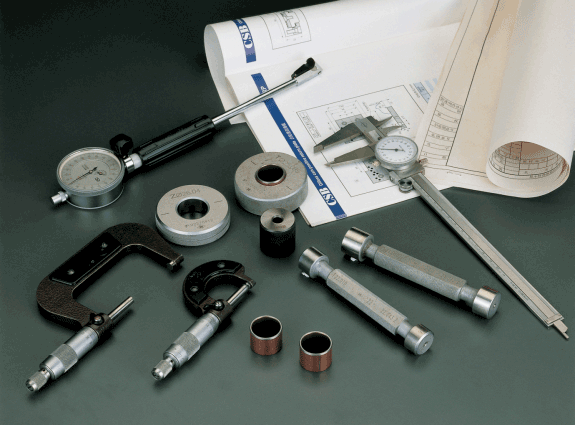
Checking the external diameter
Test A of ISO 3547 Part 2
Check the outside diameter of a wrapped bush using measuring equipment as shown in left sketch, with a checking block consisting of upper and lower halves and setting plugs, at a determined checking load of during the test the outside diameter of the bush is made smaller by the elastic reduction, however there is no permanent deformation. The bushes outside diameter can be calculated from the difference in the value of z (△z)
Test B
The test is carried out with two ring gauges, a GO ring gauge and a NO GO ring gauge whose diameter shall be chosen empirically from with Table 6 of IS03547-1:1999 and agreed upon. It shall be possible to press the bushes into the GO ring gauge and then push them through with hand pressure (maximum force 250N)_ On the other hand with the same force, it shall not be possible for them to go into the NO GO ring gauge (See ISO 12307-1)
Test D
The test is carried out by means of a precision measuring tape.
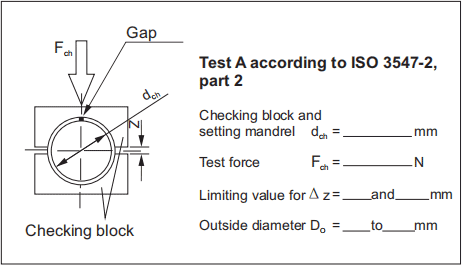
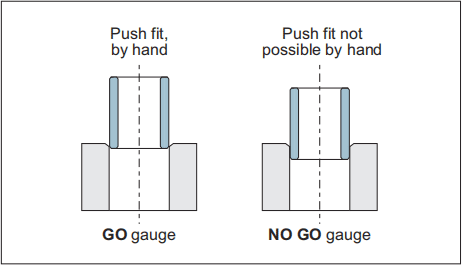
Checking the inside diameter
Test C
To check the inside diameter, the bush is to be pressed into a ring gauge, whose nominal diameter corresponds to the dimension specified in IS03547-1:999. The inside diameter shall be measured with a 3-point measuring instrument or checked with a GO and NO GO plug gauge. The GO plug gauge shall be inserted by a minimum effort; the NO GO plug gauge shall not be inserted by manual pressure (maximum force 250N). In order to enable the manufacturer and the customer to compare results of this test it should be agreed whether results should be obtained by measuring or by gauging.
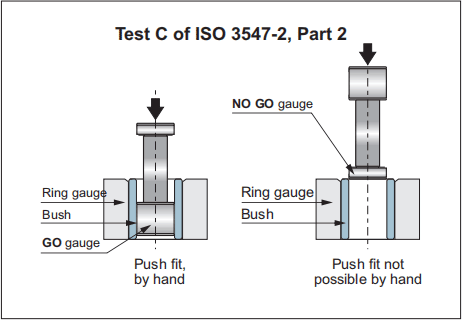
Checking the thrust washer
Beside the thickness, the flatness of a washer is of particular importance as it has impact on the life of both the washer and its mate. We use very helpful test in which the washer falls through the gap between two plain parallel plates of a gauge under its dead weight. The plates must be big enough to cover the whole washer.
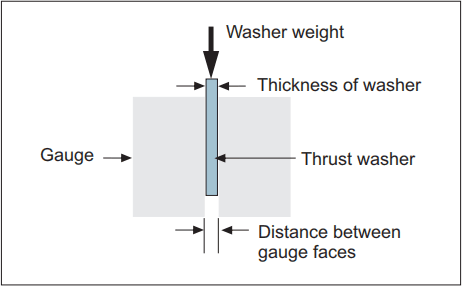
Checking the thrust washer
(alternatively to Test C)
The wall thickness is measured at one, two or three positions axially according to the bearing dimensions. The wall thickness and the inside diameter shall not be specified together on the same drawing.
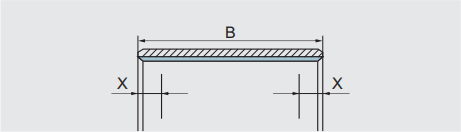
Measurement position
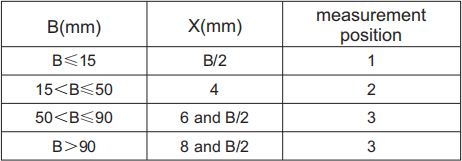